Freedom projectual
MOLD PRODUCTION
We build our tools ourselves, only with high quality steels and we test them directly in production to be sure of their production capacity.
Once the production batch is finished, we check all the molds, clean them and if necessary we revise them with our specialized staff.
Special Technology
This special technology guarantees our products:
QUALITY, VERSATILITY, PRECISION, HIGH PERFORMANCE.
This process allows a very high design freedom, as it solves the traditional molding limits of competing technologies (forging, shell casting, die casting, etc.).
With us You are more competitive
We have several models of the toecaps and sizes from 5 to 12, it will be easy for you to choose the right toecap with our drawings and our samples.
Recycling
We prepare internally our alloy with the best primary aluminium +25-35% of recycled aluminium.
Avional
Aluminium is 3 times lighter- than steel, less bulky of plastic. It’s a metal very robust with excellent corrosion resistance.
Tolerance
Our models are born from cast alloy and thus have a stable shape with a dimensional tolerance of 0.1mm instead of 0.4mm or even 0.7mm from other manufacturers.
Analyses
We chemically analyze each batch of aluminium alloy produced in our laboratory. Of course, we keep the analysis data for many years.
Weight
Optimized geometries, in addition to having better performance, also have a reduced weight of 20%.
Our lighter toecap weighs 52 grams and the heaviest only 68 grams.
Sizes
We have several models of the toecaps and sizes from 5 to 12, it will be easy for you to choose the right toecap with our drawings and our samples.
TOECAP Models & Size
Order and try our samples certified Type B.
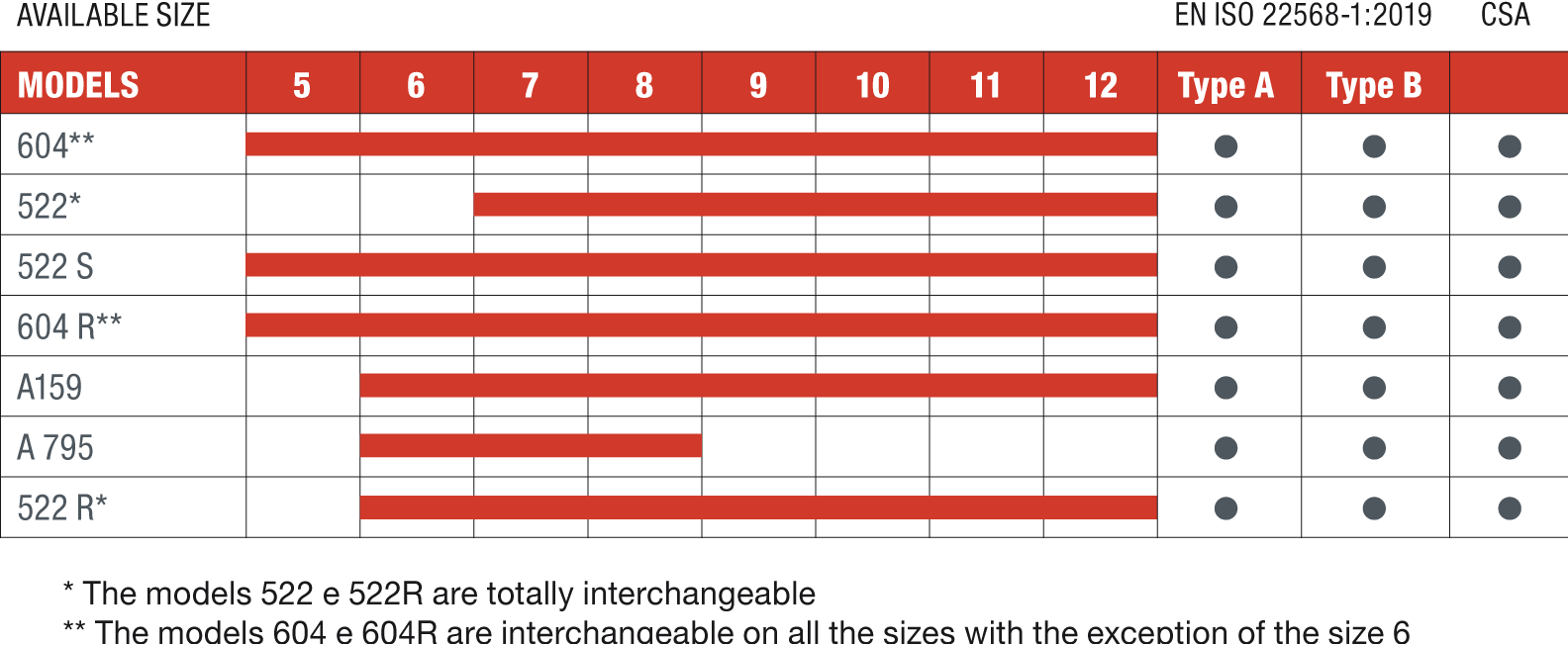
The core business of our company is represented by the production of toecaps for safety shoes, of which we hold several brands and patents. The table shows the main models of our product offer, with related sizes and homologations.
Meeting the needs of our customers is our main objective, for this reason we offer the possibility of customizing the geometries offered or developing completely new shapes.
Virtual 3D Crash test
Through our virtual crash tests we are able to verify the performance of the toecap before its realization. With our topological optimization methodologies we d efine the perfect geometry.
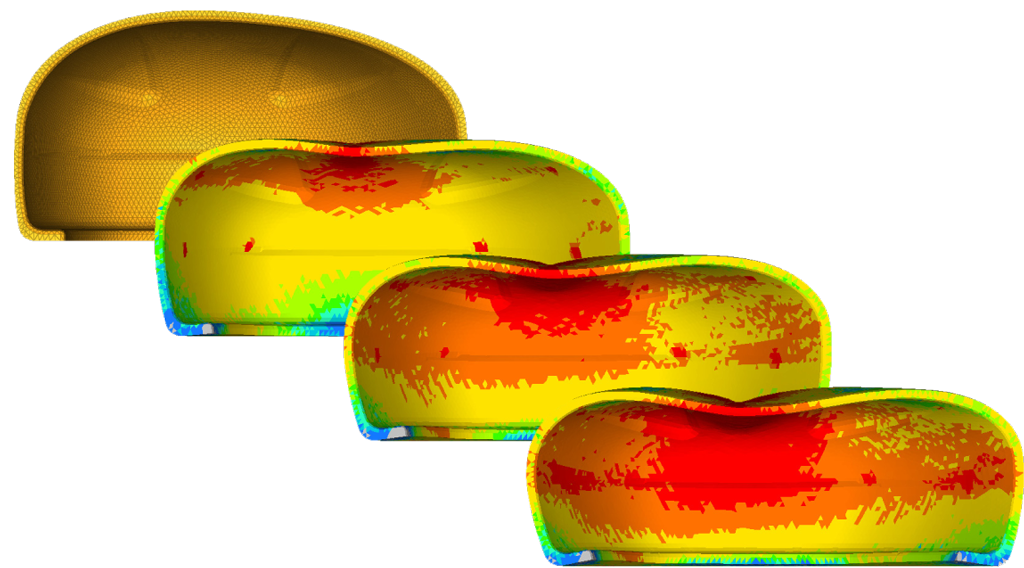
Product development
Give your ideas shape: using from the early stages of development, virtual analysis, we are able to define the perfect geometry for the style of your shoe.
The analyzes of post-crash plastic strain and Von Mises stress indicate what are the most stressed areas, allowing us to intervene on geometry so that fractures or structural failure do not occur.
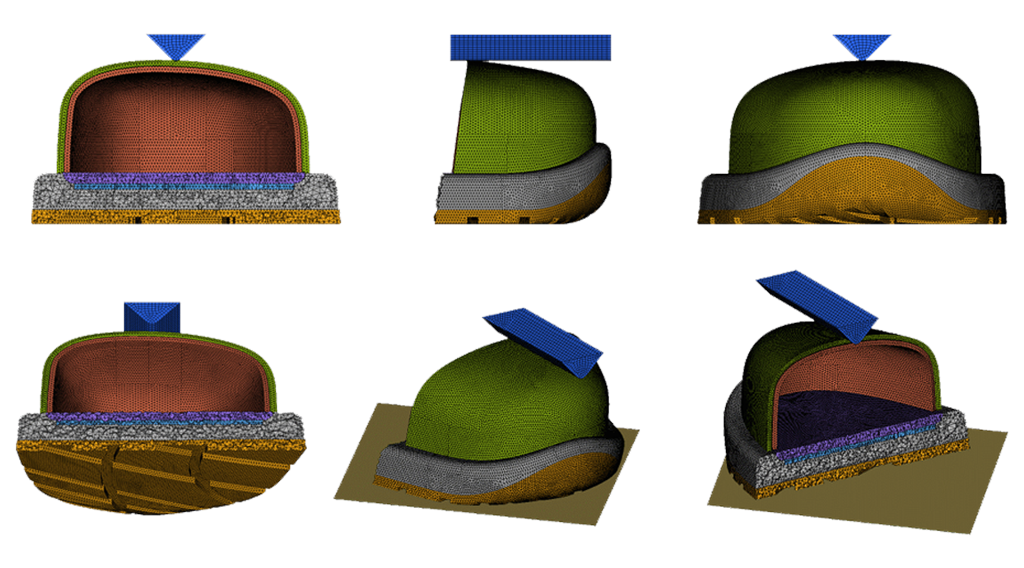
Integration
Our toecaps are verified, even before making the mold, both geometrically with the use of rapid prototyping, and functionally, with FEM simulations on a complete model (shoe + toecap).
IF YOU HAVE A NEED WE ANSWER YOU IMMEDIATELY.
IF YOU HAVE AN ISSUE WE HELP YOU SOLVE IT.
FEM Tecnology
We prefer to do well immediately and not waste time and resources with many physical tests. For this we design the toecaps with the CAD and check them with the FEM technology before building the mold.
Performance
We simulate the resistance of the toecap and if necessary we modify it to have the ideal performance.
Molds
We build our molds, only with high quality steels and try them directly in production to be sure of the production capacity.
After the production batch we check all the molds, clean them and if necessary we review them with our specialized staff.
Metallic alloy
We prepare our alloy internally with the best primary aluminium + 25-35% recycled aluminium.
We chemically analyze each batch of aluminium alloy produced, in our laboratory and we keep the data of the analyzes for many years.
Toecap weighing
We produce all our toecaps internally for all the phases of the process and weigh them all as soon as they are casted.
Only the toecaps with the right weight continue in subsequent processes because the weight is one of the quality guarantees of the toecap.
We guarantee you the weight with a tolerance of +/- 3.5 grams.
Performance
Our simulations are carried out in accordance with the European Regulation EN ISO 22568-1: 2019; The tip is positioned tangent to a 90° square, the impactor, with a weight of 20 kg, consists of a 90° shaped wedge with a 3mm radius in the impact area.
Is released by a height of 1m with an impact energy of 200 J.
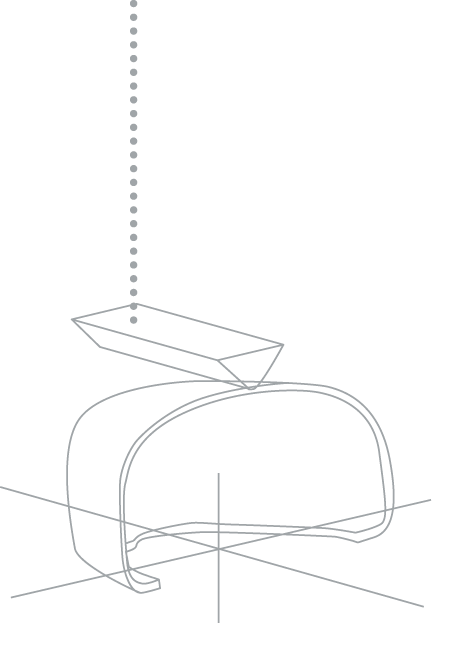
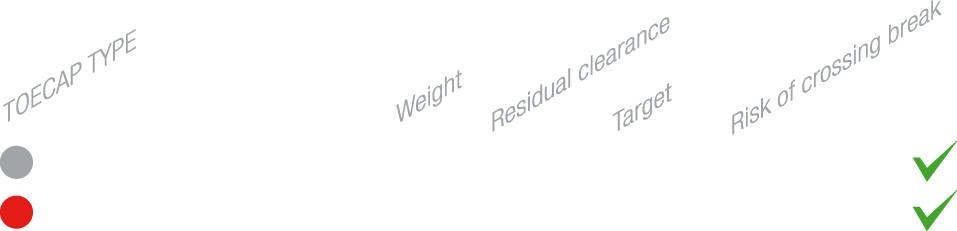
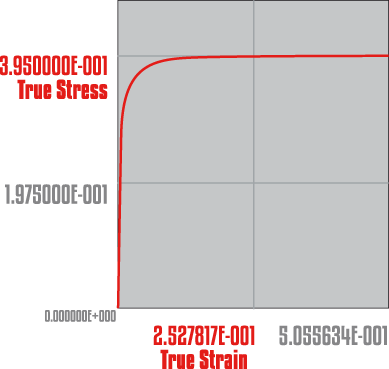
Aluminum Avional
Density 2.72 g/cm3
Tensile Strength, Ultimate 395 Mpa
Tensile Strength, Yield 230 Mpa
Elongation at Break 14 %
Modulus of Elasticity 71.0 Gpa
Poissons Ratio 0.330
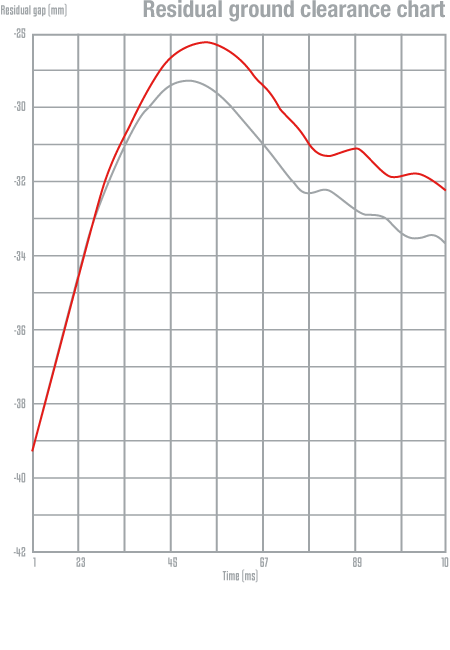